1.1 Operations Management
Operations Management and Everyday Life
Although Operations Management is often taught in business schools, one can skip business school to relate to this topic. Perhaps we can learn it by looking at the everyday life of a family living in London, Ontario.
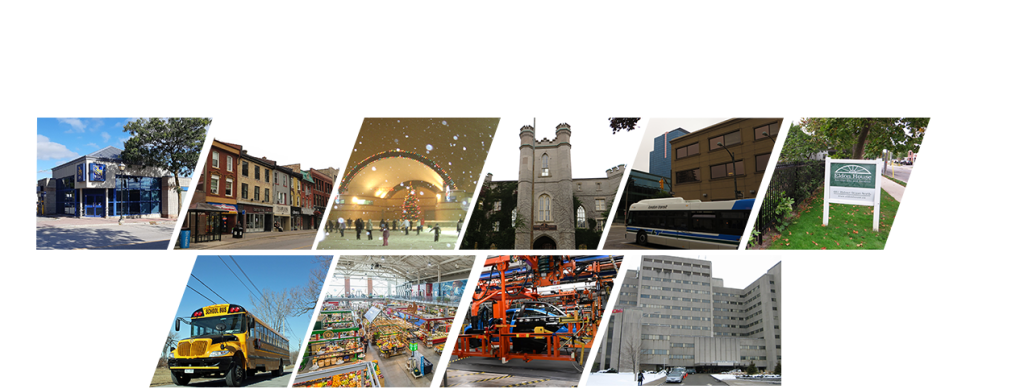
To conduct what we refer to as everyday life, they would need to do weekly grocery shopping to buy milk, meat, bread, fruit and vegetables and a few other necessities. Now, let us focus on the bread they are buying. It turns out that that bread was brought to that store in a truck from a bakery that relies on a mill to supply it with flour, which comes from a farm. The kids would have to go to school on a school bus that needs to pick them up and bring them home every day. Mom and Pop would go to work in their cars, which they had bought from a dealership and supplied by auto manufacturers. These cars needed to be maintained by a mechanic in a garage who would rely on parts and supplies delivered to his garage. The family needs to handle their finances using a bank, their garbage has to be handled by the city, and when they are ill, they need the service of a medical facility. Are these the only things this family needs to manage their daily life? Certainly not! Now, let us return to the bread they buy from their grocery store. Like you and I, they do not care “how” that loaf of bread was made available, but they certainly know “what” they need, in this case, a loaf of bread. If we want to connect the “what” to “how,” we are stepping into the field of operations management.
Operations management is a discipline that involves the processes of converting inputs into goods and services, creating value for customers. It is the foundation for any organization, ensuring efficient resource utilization in producing the products we rely on daily.
What is Operations Management
Operations management is the management of the processes that transform inputs into goods and services that add value for the customer. Consider the ingredients of your breakfast this morning. Unless you live on a farm and produce them yourself, they pass through several different processing steps between the farmer and your table and are handled by several organizations.
Every day, you use a multitude of physical objects and a variety of services. Most physical objects have been manufactured, and most of the services are provided by people in organizations. Just as fish are said to be unaware of the water that surrounds them, most of us give little thought to the organizational processes that produce these goods and services for our use—the study of operations deals with how the goods and services you buy and consume daily are produced.
The following video shows some of the basic strategic areas in operations management. We will cover some of these areas in addition to some tools and techniques used in operations management.
Video: “Operations Management” by Skillsoft YouTube [3:12] is licensed under the Standard YouTube License. Transcript and closed captions available on YouTube.
Producing Goods and Services
In the production of goods, the result is the creation of tangible products such as vehicles, articles of clothing, cell phones, or shovels. On the other hand, a service is intangible, such as a car repair, haircut, or medical treatment.
In operations management, both the production of goods and the delivery of services play crucial roles. However, there are significant differences between the two.
- Nature of Output:
- Goods: Tangible products like vehicles, clothing, cell phones, and shovels.
- Services: Intangible offerings such as car repairs, haircuts, and medical treatments.
- Customer Interaction:
- Services involve more direct customer contact. Customers either visit the service provider or vice versa.
- In manufacturing, customers rarely visit the production facility; purchases occur elsewhere.
- Labour Content:
- Services typically require more labour than manufacturing organizations.
- Input Variability:
- Services face greater input variability due to unique customer circumstances.
- Manufacturing companies deal with more standardized inputs.
- Quality Measurement:
- Manufacturing quality assessment is technical and straightforward.
- The perception of service quality depends on various factors.
- Productivity Measurement:
- Manufacturing productivity is easier to measure due to standardization.
- Services pose challenges in productivity measurement.
- Inventory Handling:
- Manufacturing can store unsold goods for later sale.
- Services lack this option; once the time passes, capacity is lost.
“1 Introduction to Operations Management” from Introduction to Operations Management Copyright © by Hamid Faramarzi and Mary Drane is licensed under a Creative Commons Attribution-NonCommercial-ShareAlike 4.0 International License, except where otherwise noted.—Modifications: used section What is Operations Management and removed first video; used section Producing Goods and Services; added introduction section
Figure 1.1.1 Image Sources
Top row L-R: “RBC Royal Bank of Canada 2“, Peter Glyn, CCO; “Downtown London, Ontario“, Ken Lund, CC BY-SA 2.0; “Victoria Park – London Ontario“, WabbitWanderer, CC BY-SA 2.0; “Middlesex County Court House, London Ontario“, Ken Lund, CC BY-SA 2.0; “Downtown London, Ontario” by Ken Lund, CC BY-SA-2.0; “Eldon House, London Ontario” by Ken Lund, CC BY-SA 2.0.
Bottom row L-R: “Canadian School Bus in Toronto“, Navjot Singh, CC BY-SA 2.0; “Covent Market, London“, Boris Kasimov, CC BY 2.0; “Door mating – Lansing Grand River automobile assembly plant production line“, Joe Ross, CC BY-SA 2.0; “University Hospital London ON“, Nephron, CC BY-SA 3.0.