11. QSE Equipment Management
In order to ensure that the laboratory’s Quality Management System is performing testing procedures that meet its’ high standard of quality, the laboratory must make certain that all the equipment used in the performance of testing meets the standards that have been set by the QMS. According to the CLSI (document GP26-A4), there are several policies that must be followed to make this happen. They include policies on each of the following criteria
- Selection and acquisition of equipment
- Equipment qualification
- A calibration program
- A maintenance program
- Decommission of obsolete equipment
- Equipment files and records
To make sure these policies are upheld, there are several processes that need to be followed. They include processes for
- the selection of equipment
- tracking the equipment in the laboratory
- Installation and operational qualifications
- Performance qualifications – validation and verification
- Authorizing staff who will use the equipment
- Perform calibrations and review results from the calibration
- Corrective action to take when the calibration fails
- Routine maintenance
- Troubleshooting, services and repair of equipment
- Decommission of equipment
- Capture and management of all equipment information, such as service records, repairs, maintenance records, etc.
The procedures that fall out from these processes include procedures for the following activities
- Selecting criteria for the required equipment
- Identifying potential hazards of the equipment and planning how to reduce any required risk
- Requesting purchase
- Initiating a master file for each piece of equipment and verifying the contents
- Recording the results of installation and operational qualifications
- Documenting results of validations and verifications, as well as authorized users
- Selecting and performing calibrations, as well as applying acceptance and rejection criteria
- Performing maintenance and function checks
- Contacting technical support and recording service and repairs performed
- Completing a decommission checklist and maintaining equipment files
Question
Can you describe some of the processes and procedures that would be required for the policy on the Calibration program?
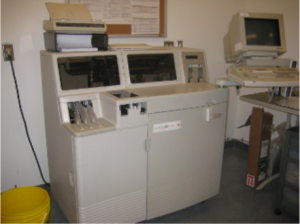
Selection of Equipment qualifications and acquisition
When a laboratory is looking to purchase a new piece of equipment, the first thing they must decide is what features the equipment needs to have in order to meet their needs. Many factors are taken into consideration when making such a decision. Some factors that must be considered include
- the volume of testing that will be performed on the equipment
- the time it takes to complete per test and per sample
- the size of the equipment because it needs to fit in the space available – the footprint
- the ventilation needs of the equipment
- the methodology of the testing
- the ease of use
- The type of training provided
- All of these factors, and possibly others, must be identified before the purchasing process can begin. Depending on the expense of the piece of equipment, there may be considerations such as pay-back time, whether to lease or buy, and how long the life expectancy might be for the equipment.
Once the list of requirements is finalized, the request for equipment goes to tender and all the offered bids are evaluated. In Canada, most of the Clinical Laboratories are funded by government so it’s important that any purchasing opportunities are seen to be open and fair and that the most economical option is chosen. Sometimes, there is a feature that may not be available on all equipment tendered, so it’s also important to make sure the selected piece has all the functionality required, from both efficiency, and safety, perspectives. For example, some automated analyzers have a cap-piercing capability that is a safety feature to protect the people loading the analyzer from coming into direct contact with the specimen. It also ensures that the specimen is protected from contamination. Depending on the tests being performed, that feature may be rated by the laboratory as a very important feature to have for the safety of staff and patients. If that is the case, the tender would state that the cap-piercing feature is highly rated on the list of requirements. The final decision as to which piece of equipment to purchase, may rest with that feature being the deciding factor. A justification must be submitted in writing to the Purchasing department (who have the final say in all purchasing decisions) as to why this feature is so important to the purchasing decision.
When the equipment is received into the laboratory, there are several specifications that must be put in place. First of all the equipment must set up and verified to perform in the manner promised. In most cases of large analyzers and other equipment, the supplier provides someone to install the equipment and to take it through the verification process to insure that it is operational.
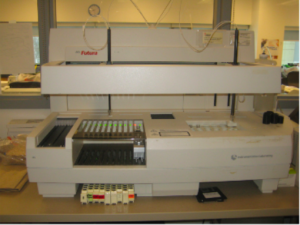
Calibration program
The next piece that must be completed before the equipment can be used for patient testing is to determine how often the calibrations must be performed and to set up the calibration program. Different pieces of equipment have different recommended calibration requirements and it falls to the purchasing laboratory to make sure that the recommendations of the supplier are followed. The calibrators must be purchased, the method evaluations performed, and the operating procedure for performing calibrations must be set up. Once all these requirements have been performed and analyzed to ensure the equipment is operational, then staff must be trained and a QC program established before patient testing actually starts.
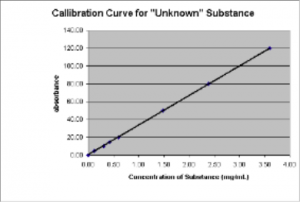
Developing the calibration curve for each analyte that is going to be run on the new analyzer is just the first step in the Calibration program. The Calibration program will actually be in place for the life of the analyzer and must be maintained and updated on a regular basis.
Maintenance program
Maintenance programs are put in place to ensure that the equipment is kept in good shape and operational for the duration of the lifespan of the equipment. To set up the maintenance program the following activities must be in place:
- Schedule of frequency for maintenance to be performed must be established and posted so that staff know when maintenance should be performed
- Scheduled maintenance responsibilities need to be assigned
- A method must be developed for performing and recording maintenance activities
- A method must be established for non-routine service and repairs. The circumstances under which the technical support will be contacted, a process and assigned responsibility for who will be the contacting person, and a log of any completed service repairs must be established.
ABL5 Maintenance
Month/Year:
Daily Maintenance | 1 | 2 | 3 | 4 | 5 | 6 | 7 | 8 | 9 | 1 0 |
1 1 |
1 2 |
1 3 |
1 4 |
1 5 |
1 6 |
1 7 |
1 8 |
1 9 |
2 0 |
2 1 |
2 2 |
2 3 |
2 4 |
2 5 |
2 6 |
2 7 |
2 8 |
2 9 |
3 0 |
3 1 |
---|---|---|---|---|---|---|---|---|---|---|---|---|---|---|---|---|---|---|---|---|---|---|---|---|---|---|---|---|---|---|---|
Check solution levels | |||||||||||||||||||||||||||||||
Check paper | |||||||||||||||||||||||||||||||
Check pressure in gas tanks | |||||||||||||||||||||||||||||||
Clean inlet | |||||||||||||||||||||||||||||||
Check waste | |||||||||||||||||||||||||||||||
Perform QC | |||||||||||||||||||||||||||||||
Initial |
Weekly Maintenance (date) | |||||
---|---|---|---|---|---|
Perform cleaning program (initial) |
Monthly Maintenance | Date and Initial When Complete |
---|---|
Re-membrane pCO2 and pO2 electrode | |
Re-membrane reference electrode |
Decommission and Final Disposal of Equipment
Once a piece of equipment has been deemed obsolete, or taken out of service permanently for other reasons, there must be an established decommissioning process to follow to make sure the piece of equipment can be safely disposed of without violating any patient confidentiality.
Equipment Files and Records
The laboratory is responsible for maintaining records throughout the life of any equipment it uses in case there is a need in the future to determine if test results produced at certain times or on particular patients, are of acceptable value. It may be necessary to prove in court that an analyzer produced results that were compliant with the manufacturer’s instruction and that quality parameters were in control on the day of a particular test being performed. Sometimes these records need to be kept for a period of time after the equipment is taken out of commission as well.
The information that must be kept on any equipment includes the following
- Calibration records
- Quality control records and documents
- Maintenance, service and repairs records, including the name of the person who performed the services, as well as the date it was performed.
- A problem log
- Date the equipment was purchased and the date it was put into service
- Where the piece of equipment was located while in operation and where it was placed after being taken out of service
- Decommissioning date and final disposal date and location
Review Questions
- What information that must be kept for the life of a laboratory analyzer?
- What are some important considerations you would take into account when selecting a piece of equipment for your laboratory?
- There are 2 very important considerations to take into account when disposing of a piece of laboratory equipment. What are they and why are they important?
- List the information that should be kept on any piece of laboratory equipment used for testing.