12. QSE Supplier and Inventory Management
The QSE for purchasing and inventory is a very important part of the quality management system. It is vital that the products and reagents used for testing are of acceptable quality if laboratories want to ensure that the testing they perform is of a high quality. If there are variations in the reagents used, or if they are unstable, that will result in less than optimal test results. Likewise, if there isn’t consistency in supplies there will not be consistency in test results. For example, semi and automated pipettes are calibrated so that the pipette will fill and expel an exact volume of liquid. If there is variation from tip to tip, the amount of sample or reagent would not be accurate and the tests would be directly affected.
According to A Quality Management System Model for Laboratory Services: Approved Guideline[1]in order to ensure this high degree of quality, there are several policies, processes and procedures in place to help laboratories meet the requirements for purchasing and inventory. Policies that apply to this QSE include the following factors that apply to purchasing and inventory
- Selection and qualifications
- Purchase of materials and services
- Supplier, contractor and consultant evaluation
- Inspection and verification of received materials
- Storage and handling of materials
- Inventory management
- Identification and tracking
There are also processes in place to ensure that the policies can be met. They include the following
- Selection of suppliers, contractors, and consultants
- Review and amendment of agreements
- Collaboration with purchasing authorities
- Selection of referral laboratories
- Provision of feedback from supplies and referral laboratories to determine if they meet the laboratory’s expectations
- Receipt, verification of performance, and the ability to trace all supplies and reagents
In order to fulfill the processes, many procedures must be in place. They include documented instructions for
- Identification of the laboratory’s expectations for products and services, as well as a procedure for comparison of supplier’s ability to meet the expectations
- Periodic reviews of purchasing agreements, directions for requesting supplies, and development of approved supplier lists
- Communication of feedback to suppliers, contractors, and consultants and a means of addressing unsatisfactory service and/or products
- Performance of verifications
- Record of lot numbers, date received, and initial inspection outcomes
- Storage and handling procedures
- Tracking inventory levels, expiry dates, and usage of materials
- Verifying acceptability of materials before using and reporting results
Meeting all of these policies, processes, and procedures requires the committed work and coordination of several departments in the organization including Purchasing, Stores, and the laboratory where the materials will be used. Each area must know the role they are expected to play and must be able to rely on the others to do their part affectively. For example, the purchasing department general deals directly with the suppliers, making sure the selection process has met standards, the stores department makes sure that all materials and suppliers are received into inventory and accounted for. The laboratory is responsible for maintaining the inventory allotted to their use and for reporting any problem that might arise with the quality of the products. Although all 3 areas may have specific roles to play, the overall QSE can only be met when the various departments communicate with one another and work together to resolve issues or problems as they arise.
Ability to meet Requirements
Before any particular company can be selected to provide supplies and/or services, the Laboratory, in conjunction with the purchasing department, must determine what qualifications and specifications are required of any company they plan to deal with. Since the Laboratory has a QMS in place, they will want to make sure the suppliers they approve also have a certified QMS designation such as ISO 9001. They will want to research the company to ensure that the supplier has a good reputation for reliability and providing good service. The Laboratory should make up a list of their requirements and share these with Purchasing who will look after determining the final list of criteria.
Items that the laboratory may want to take into consideration would include such items as:
- Stability of reagents to ensure that they will be usable once received in the lab
- The company’s reputation for service – do they offer timely replacement when there is an issue with any of their products?
- Length of time to receive orders once they have been placed – does the company have an issue with “back orders? How far away are they? How much do they charge for shipping and handling?
Question
What are some of the problems that could arise if the Laboratory used a supplier who could not meet their requirements?
Purchase of Materials or Services
There are a number of criteria that must be in place before the laboratory agrees to use the services or supplies of a given supplier. Typically, there will be a written agreement that is signed off by both parties agreeing to the needs and responsibilities of both the laboratory and the supplier. These agreements are for a set period of time and must be reviewed and amended according to the agreed upon schedule. For example, some high volume, standard supplies used by all lab disciplines may have agreements in place for short periods because of the fluctuating prices often seen in the industry. Gloves, pipette tips, and other standard items that are broadly used could have their agreements reviewed and amended as often as every 3 months. Other agreements for more specialized items, such as reagents and analyzer specific consumables may have agreements that are in effect for 1 year or more. Typically, the level of specialization has an impact on these decisions and may be dependent on several factors, such as the length of the contract on the analyzer or the volume of testing performed within the agreement period. The higher the testing volume is, the lower the unit price.
Agreement must also be established with the purchasing department as to which responsibilities fall on the laboratory and which are under the domain of the purchasing department. For example, there must be clear understanding about who is responsible for tracking inventory and ordering more supplies when they start to run low. Depending on the type of agreement that was set in place, that responsibility may fall to the Laboratory or may stay with the Purchasing dept. Quite often agreements are set up that say how much of a particular reagent will be purchased throughout the year but arrangements are put in place to have deliveries made periodically throughout the year. This helps ensure that reagents do not expire while in stock and that the company can offer its most competitive rates based on an annual volume. When this type of arrangement is put in place, it may well be the responsibility of the Laboratory to order shipments as supplies start to get used up. They are the people in the best position to know what their needs are and to determine their testing volume is at any given time.
Purchasing testing services at a referral laboratory also falls under the purchase of Materials and Supplies. The Laboratory must make sure that the laboratories where they send their referral specimens are credible and also participate in QMS. Generally, these agreements are reviewed annually to make sure the continuing service lives up to expectations of the purchasing laboratory.
The Laboratory is also responsible for providing feedback to the suppliers, consultants and contractors who provide service to them. They need to be made aware of whether or not they are meeting the laboratory’s satisfaction, and if they aren’t, they need to know what changes or revisions would be required to keep them competitive.
Question
What are some areas where suppliers might not be living up to expectations?
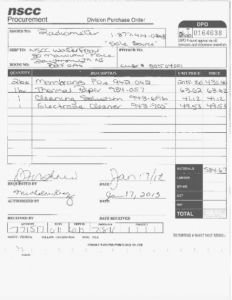
Inspection and verification of received goods
Inspection and verification of received goods are an important aspect of receiving materials. When supplies first arrive on site at the laboratory, it is important that they are checked over to make sure that the correct goods were shipped and that they weren’t damaged in shipment. If the laboratory fails to do this inspection, they have no recourse to go back to the supplier with complaints that goods were substituted or broken. Once they have been received and put into use, they are the responsibility of the end user. The laboratory also needs to verify that the goods they received are the ones that the Stores department sent them, and the same ones that Purchasing ordered.
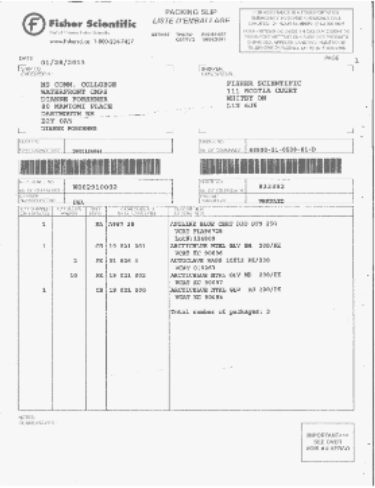
Storage and handling of supplies
Obviously it is the responsibility of the receiving laboratory to make sure that goods received by them are then stored under appropriate conditions. For example, if the goods require refrigeration or being kept frozen, it is the laboratory’s responsibility to make sure that happens. Likewise, when the supplies are first received in Stores, it is their responsibility to either store the supplies correctly according to specifications or to deliver them immediately to the requesting Laboratory so that they can be placed in proper storage.
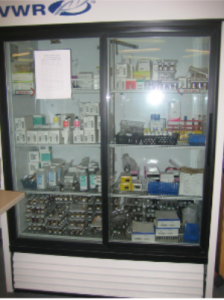
Inventory Management
Inventory Management is another important aspect of this QSE that must be taken under consideration. The laboratory has several criteria that all reagents and many other supplies that must be tracked. Although Stores may be responsible to maintaining the inventory for some supplies, anything coming into the laboratory must be inventoried at that point.
Question
For example, what are some of the pieces of information that are of importance in the laboratories where you completed your clinical placements?
Question
Typically, the date of receipt and the lot number of supplies and reagents are tracked. It becomes the responsibility of the testing laboratory to make sure they move inventory so that the oldest materials are used up before newer supplies are taken. It is also vitally important to make sure a new lot number of reagent is not placed into use before all the old reagent is used up. Once a new reagent is placed into services, what must be completed before testing procedures can be resumed?
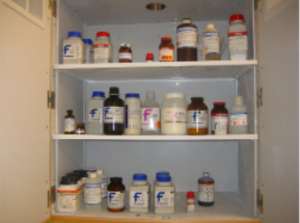
Identification and Tracing of Critical Materials and Services
The reason critical supplies and services must be traceable are because they are vital to the success of the laboratory’s testing process. Some of the reagents that might fall into this category include items that must be kept frozen or refrigerated, reagent kits, calibrators, controls and blood products. If any of these items get lost during the shipping process or have to be backordered, it can cause extensive disruption to the work of the laboratory. Testing may be delayed or sometimes even have to be shipped to another laboratory.
The other reason it’s necessary to trace supplies is to ensure they are getting used before they expire and to check that all of one lot number gets used up before the next lot number is put into use. Otherwise, calibrations may be run unnecessarily which increases the overall workload and adds to the total expenses of the lab.
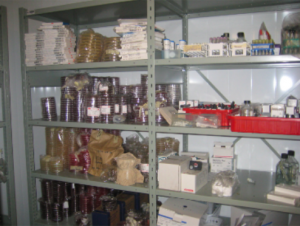
Review Questions
- How should reagents be stored once they are received in the Lab?
- Near the bench where they will be used
- In the refrigerator
- On low shelves to prevent back injury
- According to manufacturer’s instructions
- What must a supplier do in order to be considered as a potential supplier to the Lab?
- Have a certified QMS in place
- Offer the most competitive prices
- Have a good returns policy
- Supply reagents with the longest shelf life
- What is required to maintain adequate amounts of supplies and reagents on hand?
- A good supplier list
- A good inventory management system
- Good supply agreements
- A good mechanism for tracing critical materials
- Which of the following items is not a consideration when selecting a supplier?
- Stability of reagents
- The size of the company
- The company’s reputation
- Delivery time for orders
- Which of the following parties is NOT part of the Purchasing agreement?
- The Laboratory
- The purchasing dept.
- The hospital’s management
- The supplier
- p.61, ↵